Causes of O-ring failure
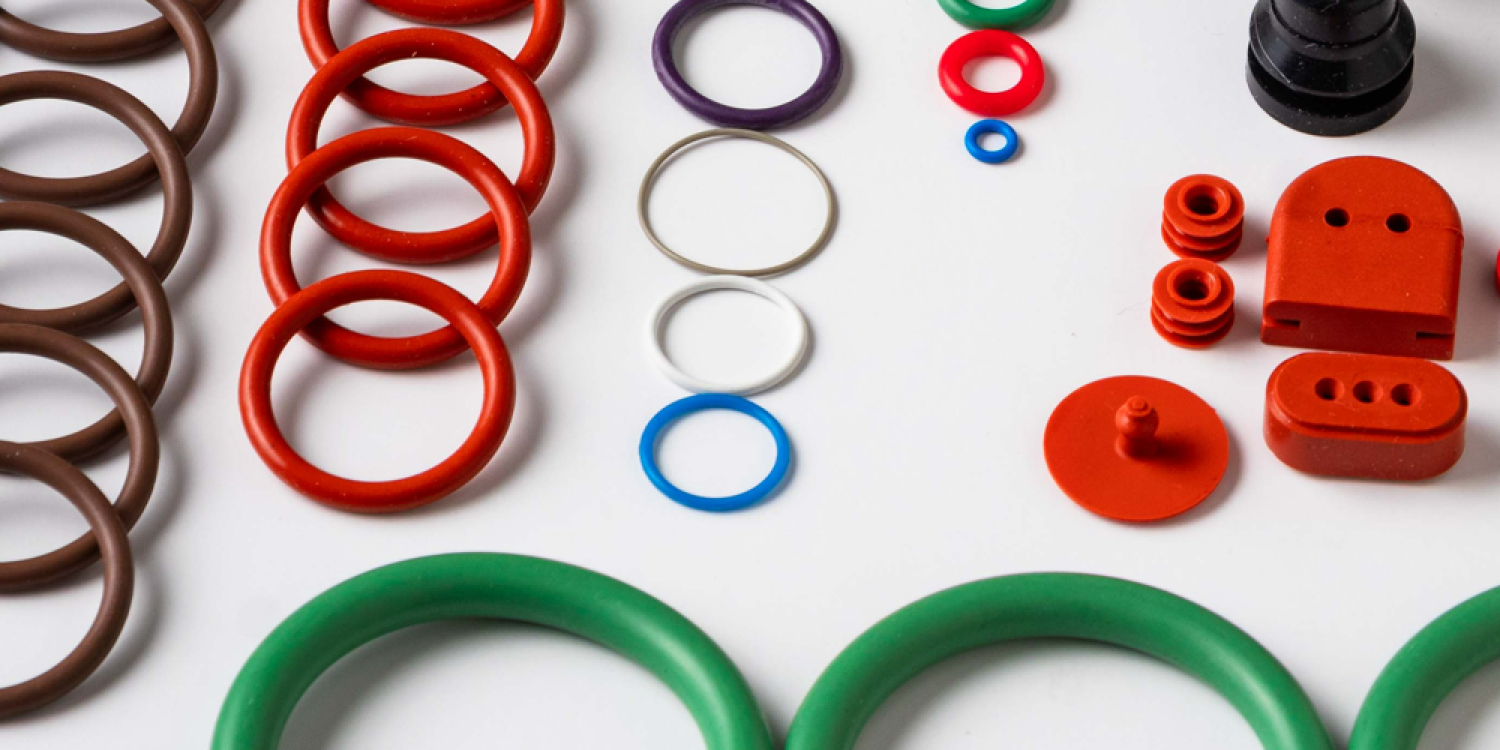
O-ring failure can result from a variety of factors, often identified by their appearance and underlying causes. Here's a breakdown of common causes:
♦ Physical Damage During Installation:
1. Cutting or Nicking: Sharp edges on mating components, burrs, or using of incorrect installation tools can easily cut or nick the O-ring.
2. Pinching or Rolling: If the O-ring is not properly placed during assembly, it can become pinched or rolled, leading to a distorted shape and eventual failure.
3. Excessive Stretching: Overstretching the O-ring during installation can cause tearing or weaken its elasticity, leading to failure.
4. Contamination: The presence of dirt, debris, or metal particles on the O-ring or sealing surfaces can cause abrasion and prevent the formation of a proper seal.
♦ Extrusion and Nibbling:
1. High Pressure: If system pressure exceeds the O-ring's hardness and the clearance gap between mating components is too large, the O-ring material may be forced into the gap. Pressure fluctuations can then cause a "nibbling" effect, gradually damaging the O-ring.
2. Excessive Clearance Gaps: Large clearance gaps allow room for the O-ring to extrude when exposed to pressure, increasing the risk of failure.
3. Soft O-ring Material: O-rings made of softer materials are more vulnerable to extrusion under high pressure due to their lower resistance to deformation.
♦ Abrasion and Wear:
1. Dynamic Applications: In systems with moving components, continuous friction between the O-ring and mating surfaces can lead to gradual wear over time.
2. Rough Surface Finish: A metal surface that is too rough can behave like sandpaper, accelerating wear on the O-ring.
3. Insufficient Lubrication: Without adequate lubrication, friction increases, which leads to faster wear and potential damage to the O-ring.
4. Abrasive Particles: Contaminants present in the system fluid can act as abrasive agents, causing the O-ring to wear down prematurely.
♦ Compression Set:
1. High Temperatures: Elevated temperatures can accelerate the degradation of the O-ring material, impairing its ability to return to its original shape being compressed.
2. Excessive Compression: Over-compressing the O-ring during installation, beyond its design specification can result in permanent deformation.
3. Poor Material Selection: The use of a material that lacks adequate resistance to compression set, unsuitable for the application’s conditions, can lead to failure.
4. Prolonged Static Sealing: Even in static applications, long-term compression can cause the O-ring to undergo permanent deformation.
♦ Chemical Degradation and Swelling:
1. Incompatible Fluids: The O-ring material may react adversely with the system fluid, leading to swelling, shrinking, hardening, softening, or even dissolution.
2. Concentration and Exposure Time: Elevated chemical concentrations and extended exposure periods significantly heighten the risk of degradation.
3. Temperature Effects: Higher temperatures can exacerbate chemical reactions, further compromising the O-ring’s integrity.
♦ Thermal Degradation and Oxidation:
1. High Temperatures: Exceeding the O-ring material's temperature limits can cause it to harden, crack, and lose elasticity.
2. Exposure to Oxygen and Ozone: Oxidation reactions can lead to the aging and embrittlement of the rubber material.
3. UV Exposure: Prolonged exposure to ultraviolet light can degrade the O-ring, reducing its performance and lifespan.
♦ Spiral Failure (Twisting):
1. Uneven Lubrication: In dynamic applications, inconsistent lubrication can cause parts of the O-ring to stick, resulting in twisting.
2. Extreme Speed: Both excessively high and very low reciprocating speeds can contribute to spiral failure.
3. Incorrect O-ring Size: Using an O-ring with the wrong cross-section for the groove can increase the risk of twisting.
4. Excessive Clearance: Large clearances in the gland design allow the O-ring to roll and twist.
♦ Explosive Decompression:
1. High-Pressure Gas Applications: In environments with high-pressure gas, the gas can gradually permeate the O-ring material. If the pressure is suddenly released, the rapid expansion of the trapped gas can cause blistering, cracking, or even rupture of the O-ring.
A clear understanding of these causes is essential for selecting the correct O-ring material and size, designing suitable sealing glands, applying proper installation methods, and maintaining the system effectively, as it helps prevent premature failures and ensures long-term system integrity.